Gas firing
I really like the effects of stoneware reduction firing especially for shino glazes so I thought that I would have a go at building a small gas-fired kiln for the garden to investigate whether it would be possible to achieve a firing on a small scale
|
I based the design on photos in Ian Gregory's book Alternative Kilns (A&C Black 2005) for the raku rocket on the basis that this should be reasonably gas tight and easy to insulate. The liner components, chamber, lid and flue, were thrown using a succession of large coils to build up the height and then separately thrown ports added.
| |
|
The lid and chamber were too large to fit in our electric kiln so they were fired by building a flat pack kiln arund them. |
Once fired, the chamber and lid were insulated with ceramic fibre, aluminium sheet and weldmesh or chicken wire so that firing could commence
| |
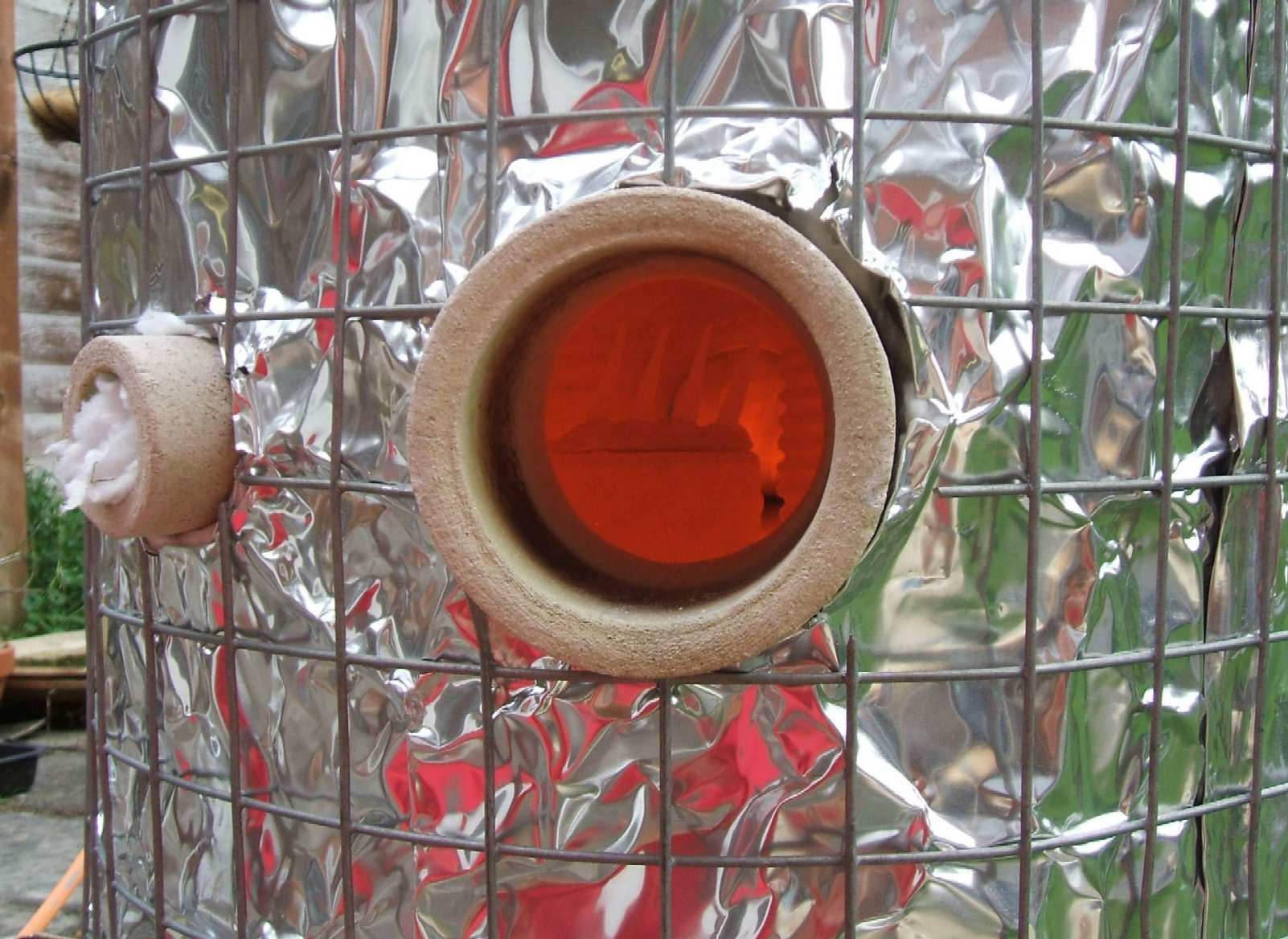 |
Temperature monitoring was via cones and the pyrometer. The ports were sealed with ceramic fibre and reduction was controlled via the gas supply and a kiln shelf damper on the flue. The kiln had diificulty getting up much above 1150oC
|
After firing the kiln was stopped up and left to cool overnight. This is a view through the flue vent in the lid. The reduction was not very strong but the two mugs with a shino glaze came out quite well with a range of greens, greys and silver indicating some carbon capture
| |
|
|
|
|